. In this case the two sensors use the same technology. The two channels are homogeneous. This may increase the possibility of common cause failures compared to the solution Encoder + Proximity, making it more difficult to achieve the minimum score (65) of the CCF factor. This is a dual channel solution and the fault is detected due to the. Other Sensors and Sensor Accessories; Accelerometer Cables; Accelerometer Mounting Accessories; Speed Sensors; Shaft Riders and Accessories; Safety Barriers and Enclosures; Entek 2100 Series Probe Systems; 2100 Series Proximity Probes; 2100 Series Extension Cables; 2100 Series Probe Drivers; Kits; ViSTeC Portable Overall Meter; Enpac Portable.
- Plc Motor Encoder Proximity Sensor Circuit
- Plc Motor Encoder Proximity Sensor Wiring
- Plc Motor Encoder Proximity Sensor Kit
- Plc Motor Encoder Proximity Sensor
In PLC control system, we mostly use DC proximity sensors. And in DC circuit, the proximity sensors used include 2-wire proximity sensor, 3-wire proximity sensor and 4-wire proximity sensor. And they can be further divided into NPN type and PNP type. Generally, people in the United States and Japan usually use NPN proximity sensor, while in the Europe use the PNP proximity sensor.
Plc Motor Encoder Proximity Sensor Circuit
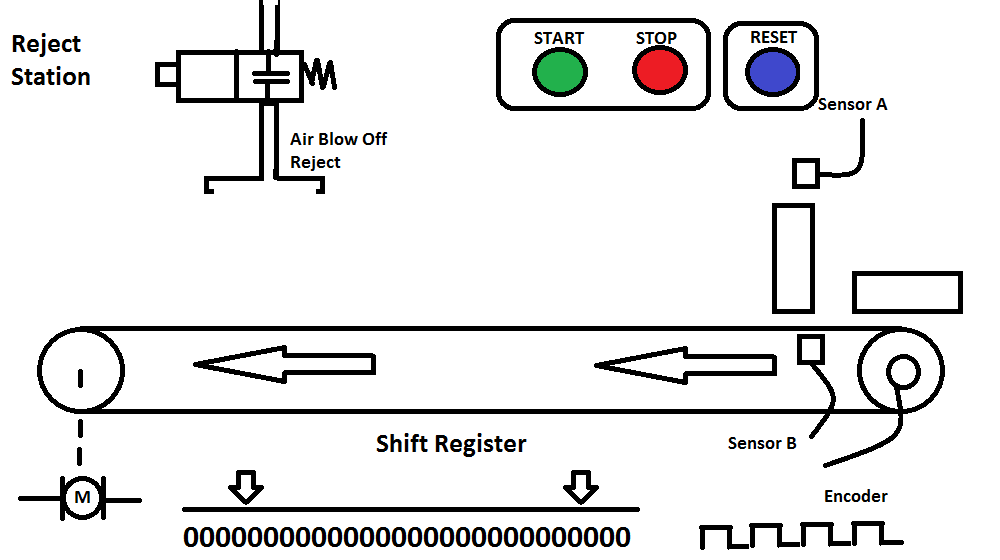
The difference of NPN proximity sensor and PNP proximity sensor lies in the conduction situation. NPN proximity sensor belongs to the low level conduction and PNP proximity sensor belongs to the high level conduction. In other words, signal of the NPN proximity sensor flows from the load to the proximity sensor, while that of the PNP proximity sensor flows from the proximity sensor to the load.
We will take FX3U PLC and S7-200 PLC as examples to explain how is the NPN proximity sensor and PNP proximity sensor connected to PLC. According to the wiring diagram of proximity sensor, we should first find out the load in the PLC.
The common port of PLC signal input and signal input can be taken as two ends of a load, then the wire connection can be completed according to the wiring diagram of proximity sensor and the difference of NPN proximity sensor and PNP proximity sensor.
1. Wire connection of FX3U PLC and 3-wire NPN proximity sensor
NPN proximity sensor is characterized as low level conduction, its signal flows from the load to the proximity sensor. But the signal output wire of proximity sensor must be connected to the signal input point of PLC, so when a NPN proximity sensor is connected, the signal flows from the input signal terminal of PLC, and the other end of load (namely the common port COM) shall be connected to the high level (namely the 24V+). In this way, the signal flows out from the input point. The wire connection diagram is shown as follow:
A 24V sensor power supply on PLC can be used as the power supply, external power supply can also be used.
2. Connect 3-wire NPN proximity sensor to S7-200 PLC
3. Wire connection of S7-200 PLC and 3-wire PNP proximity sensor
Plc Motor Encoder Proximity Sensor Wiring
In PLC control system, we mostly use DC proximity sensors. And in DC circuit, the proximity sensors used include 2-wire proximity sensor, 3-wire proximity sensor and 4-wire proximity sensor. And they can be further divided into NPN type and PNP type. Generally, people in the United States and Japan usually use NPN proximity sensor, while in the Europe use the PNP proximity sensor.
The difference of NPN proximity sensor and PNP proximity sensor lies in the conduction situation. NPN proximity sensor belongs to the low level conduction and PNP proximity sensor belongs to the high level conduction. In other words, signal of the NPN proximity sensor flows from the load to the proximity sensor, while that of the PNP proximity sensor flows from the proximity sensor to the load.
We will take FX3U PLC and S7-200 PLC as examples to explain how is the NPN proximity sensor and PNP proximity sensor connected to PLC. According to the wiring diagram of proximity sensor, we should first find out the load in the PLC.
The common port of PLC signal input and signal input can be taken as two ends of a load, then the wire connection can be completed according to the wiring diagram of proximity sensor and the difference of NPN proximity sensor and PNP proximity sensor.
1. Wire connection of FX3U PLC and 3-wire NPN proximity sensor
NPN proximity sensor is characterized as low level conduction, its signal flows from the load to the proximity sensor. But the signal output wire of proximity sensor must be connected to the signal input point of PLC, so when a NPN proximity sensor is connected, the signal flows from the input signal terminal of PLC, and the other end of load (namely the common port COM) shall be connected to the high level (namely the 24V+). In this way, the signal flows out from the input point. The wire connection diagram is shown as follow:
A 24V sensor power supply on PLC can be used as the power supply, external power supply can also be used.
Plc Motor Encoder Proximity Sensor Kit
2. Connect 3-wire NPN proximity sensor to S7-200 PLC
Plc Motor Encoder Proximity Sensor
3. Wire connection of S7-200 PLC and 3-wire PNP proximity sensor